지난 2년(2015년, 2016년)은 항공우주 산업 내 DMP(Direct Metal Printing)의 티핑 포인트로 볼 수 있습니다. 3D 프린팅 기술이 원형 제작을 넘어 비행이 가능한 생산 부품 및 어셈블리로 점점 더 많이 진출했기 때문입니다.
이 기간 동안 Airbus Defence and Space는 3D Systems와 협력하여 획기적인 성과를 거두었습니다. 상업용 통신 위성에서 사용하기 위해 테스트 및 검증된 최초의 3D 프린팅 무선 주파수(RF) 필터가 그것입니다. 이 프로젝트는 유럽우주국(A0/1-6776/11/NL/GLC: Modelling and Design of Optimised Waveguide Components Utilising 3D Manufacturing Techniques)에서 자금을 지원받은 연구에 기초했습니다.
금속 RF 또는 도파관 필터는 50여년 전 최초의 우주 통신 시스템까지 거슬러 올라갑니다. 이러한 필터는 교통 경찰 같은 역할을 하여 선택된 채널의 주파수를 통과하게 하고 선택된 채널 외부 신호의 주파수를 거부합니다.
주요 산업 경향은 단일 위성 내에 여러 빔의 용량을 늘리는 것입니다. Airbus Defence and Space에서 제조한 Eutelstat KA-SAT와 같은 고용량 위성은 RF 필터 약 500개와 도파관 600개 이상을 운반합니다. 이 중 대부분은 특정 주파수 처리를 위해 맞춤 설계되었습니다.
중요 요구 사항 충족
통신 위성은 항공우주 산업에서 끊임없이 강조하는 경량화를 잘 보여줍니다. 발사체를 정지 궤도에 보내는 데는 km당 최대 20,000달러의 비용이 들 수 있습니다. 지속적인 설계 혁신과 생산 시간 단축도 중요한 우선순위입니다. 대부분의 위성이 10~15년을 수명으로 설계되기 때문입니다.
이러한 우선순위로 인해 통신 위성은 Direct Metal Printing의 이상적인 후보입니다. Airbus RF 필터 프로젝트에 사용된 3D Systems ProX® DMP 320으로 제조업체는 부품을 통합하고 기존 방법으로는 제조 불가능한 형상과 표면을 사용해 기능을 개선하며 맞춤 설계를 위한 생산 시간 단축 및 비용을 절감하고 소재 강도를 유지하거나 개선하면서 중량을 줄일 수 있습니다.
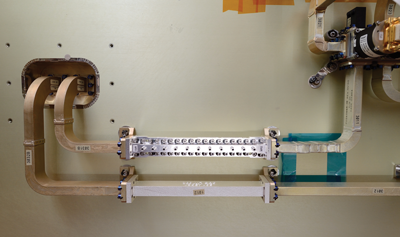
검증된 프린터의 새로운 응용 분야
벨기에 루뱅에 있는 3D Systems 시설에서는 3D Systems ProX DMP 320이 베타 단계에 있던 때부터 이 기계를 사용하고 있습니다. 성공적인 프로젝트에는 우주비행 검증 부품(예: 통신 위성용 브래킷과 스트러트 엔드 피팅)의 토폴로지 최적화, 경량화, 부품 통합이 포함됩니다. Airbus Defence and Space 프로젝트는 3D Systems Leuven이 RF 필터 분야에 진출한 첫 사례입니다.
Prox DMP 320은 까다로운 24/7(연중무휴) 생산 환경에서 높은 정밀도와 처리량을 제공하도록 설계되었습니다. 다양한 LaserForm 합금(티타늄, 스테인레스 스틸, 알루미늄, 니켈 크로뮴, 코발트 크롬)이 본 금속 프린터용으로 제조 및 미세 조정되어 고품질 부품과 일관된 속성을 제공합니다.
교환 가능한 제조 모듈은 다양한 부품 소재 사이에서 이동할 때 응용 분야의 다목적성을 높이고 가동 중단 시간을 줄입니다. 제어된 진공 제작 챔버는 모든 부품이 검증된 특성, 밀도 및 화학적 순도로 프린트되도록 합니다.
파괴적인 설계 혁신
Airbus Defence and Space RF 필터 프로젝트는 수십 년 동안 눈에 띄는 변화가 없었던 항공우주 부품의 새로운 설계 혁신을 가능하게 한 3D 프린팅의 능력을 보여줍니다.
RF 필터는 전통적으로 직사각형 캐비티, 수직 굴곡이 있는 도파관 단면과 같은 표준화된 요소의 라이브러리에 기반하여 설계되었습니다. 형상 및 연결은 밀링과 스파크 침식 등의 일반적인 제조 공정에 좌우됩니다. 그 결과 RF 필터의 캐비티는 일반적으로 볼트로 결합된 두 개의 반쪽으로 가공해야 합니다. 이렇게 되면 중량이 늘고 어셈블리 단계가 생산 시간에 추가되며 추가적인
품질 평가도 필요합니다.
3D 프린팅용 부품 설계로 Airbus Defence and Space는 추가적인 제조 비용 없이 복잡한 기하형상을 탐색할 수 있었습니다.
표준 3D 전자기 시뮬레이션 소프트웨어 도구인 CST MWS가 최적화에 시간을 거의 들이지 않고 3D 프린팅 RF 필터를 설계하는 데 사용되었습니다. 3D 프린팅으로 높아진 제조 유연성은 눌린 초타원체의 캐비티를 사용하는 설계로 이어졌습니다. 고유한 형상은 RF 전류를 전달하고 Q 요인(손실된 에너지에 기반한 도파관의 효율성 측정치)과 대역 외 신호
거부 간에 필요한 균형을 제공하는 데 도움이 되었습니다.
"파괴적인 혁신은 이제 제조 가능성이 아니라 순수한 기능이 하드웨어가 어떻게 설계될지를 판가름한다는 사실에 있습니다", 루뱅 소재 3D Systems의 프로젝트 엔지니어인 Koen Huybrechts 씨의 설명입니다. "이 프로젝트는 '형태는 기능을 따른다'를 보여주는 전형적인 예입니다."
"3D 프린팅으로 가능해진 모놀리식 설계의 주요 이점은 질량, 비용, 시간입니다", 영국 스티브니지에 위치한 Airbus Defence and Space의 RF 엔지니어인 Paul Booth 씨의 말입니다. "질량은 더 이상 고정 장치가 필요 없기 때문에 줄어듭니다. Direct Metal Printing을 사용하면 외부 프로파일이 내부 프로파일을 보다 가깝게 따르는 비용이 들지 않는 장점도 있어서 꼭 필요한 금속만 사용하게 됩니다. 비용/시간 이점은 어셈블리 및 후처리 감소의 결과입니다.
표면 문제 제거
초기에는 3D 프린팅 금속 부품의 다양한 표면 토폴로지가 문제가 된다고 생각했고 Airbus Defence and Space에서 시행한 광범위한 테스트로 이러한 문제를 제거했습니다.
"미세한 토폴로지는 가공 부품에서보다 3D 프린팅 부품에서 다양합니다", Booth 씨의 말입니다. "가공된 표면은 날카로운 고점과 저점이 있는 반면 3D 프린팅 표면은 융화된 회전타원체이므로 날카로움이 덜합니다."
"3D 금속 프린팅에 사용된 분말 입자의 구 형상은 급격한 전환보다는 특정 파형을 일으킵니다", Huybrechts 씨의 설명입니다. "그러나 더 효과적인 신호 필터링을 위한 부품 형성 능력 덕분에 표면 토폴로지 관련 문제를 극복합니다."
"3D Systems의 작업에 정말 만족했습니다. Airbus 내부에서도 훌륭한 표면 마감 처리가 많이 언급되었습니다", Booth 씨의 말입니다. "x-레이 CT 스캔을 했는데 부품 밀도와 전체적인 표면 품질에 깊은 인상을 받았습니다."
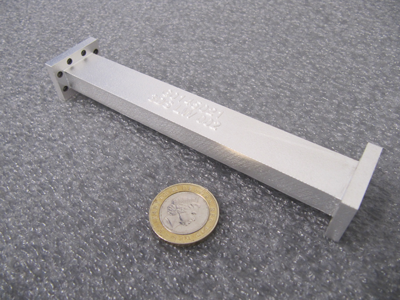
엄격한 테스트 통과
다양한 처리 경로를 사용하여 ProX DMP 320으로 프린트된 세 가지 알루미늄 샘플을 Airbus Defence and Space의 스티브니지 시설에서 테스트했습니다. 테스트는 진동, 충격 및 열 상황(예: 극한의 온도 및 진공 조건)을 비롯하여 부품이 발사 및 궤도를 도는 동안 부딪힐 조건을 모방했습니다. 세 가지 샘플은 전해 공정을 통해 은으로 도금된 필터에서 나오는 최고의 성능으로 모두 요구 사항을 충족하거나 초과했습니다.
3D 프린팅 외에도 3D Systems는 인증된 분말 취급, 우수한 소재 밀도를 위한 공정 제어, 검증된 후처리 및 신뢰할 수 있는 품질 관리 등 이러한 종류의 프로젝트에 중요한 부가 가치를 제공했습니다.
Booth 씨는 이렇게 추가된 전문성이 프로젝트의 성공에 주요 역할을 했다고 인정합니다. "프로젝트의 성공은 단순히 부품 제조에 좋은 기계를 사용해서만이 아니라 제조 공정에 관한 3D Systems의 이해도가 높은 결과이기도 합니다."
대규모 ROI 잠재력
이제 공정이 검증되고 부품이 Airbus Defence and Space에서 정한 가장 높은 우주비행 표준을 충족했으므로 회사는 3D 프린팅의 투자 수익 잠재력을 고려할 수 있습니다. 프로젝트는 CFO의 눈에 희망적인 ROI를 전달했습니다. 처리 시간 단축, 생산 비용 절감, 50%라는 놀라운 경량화가 바로 그것입니다.
"최적화에 시간을 조금도 쓰지 않고 질량을 줄였기 때문에 더 공격적인 기계 설계로 추가로 더 줄일 수 있습니다", Booth 씨의 말입니다. 감소된 질량으로 로켓에 필요한 추진제가 줄어 비용이 절감되고 지지 구조물에 대한 요구도 줄면서 질량 감소가 추가될 수 있습니다.
"이 프로젝트의 성공으로 RF 필터를 기계 및 열 구성 요소와 대규모로 통합하여 부품 수와 전체 질량을 줄일 가능성이 열렸습니다. 테스트 커플러와 같은 더 많은 기능을 필터의 일부로 통합하거나 도파관로에 직접 통합하는 것을 고려할 것입니다. 질량을 줄이는 동시에 생산 시간과 비용을 절감할 수 있는 가능성이 상당합니다."